Understanding TPU Filament: A Comprehensive Guide
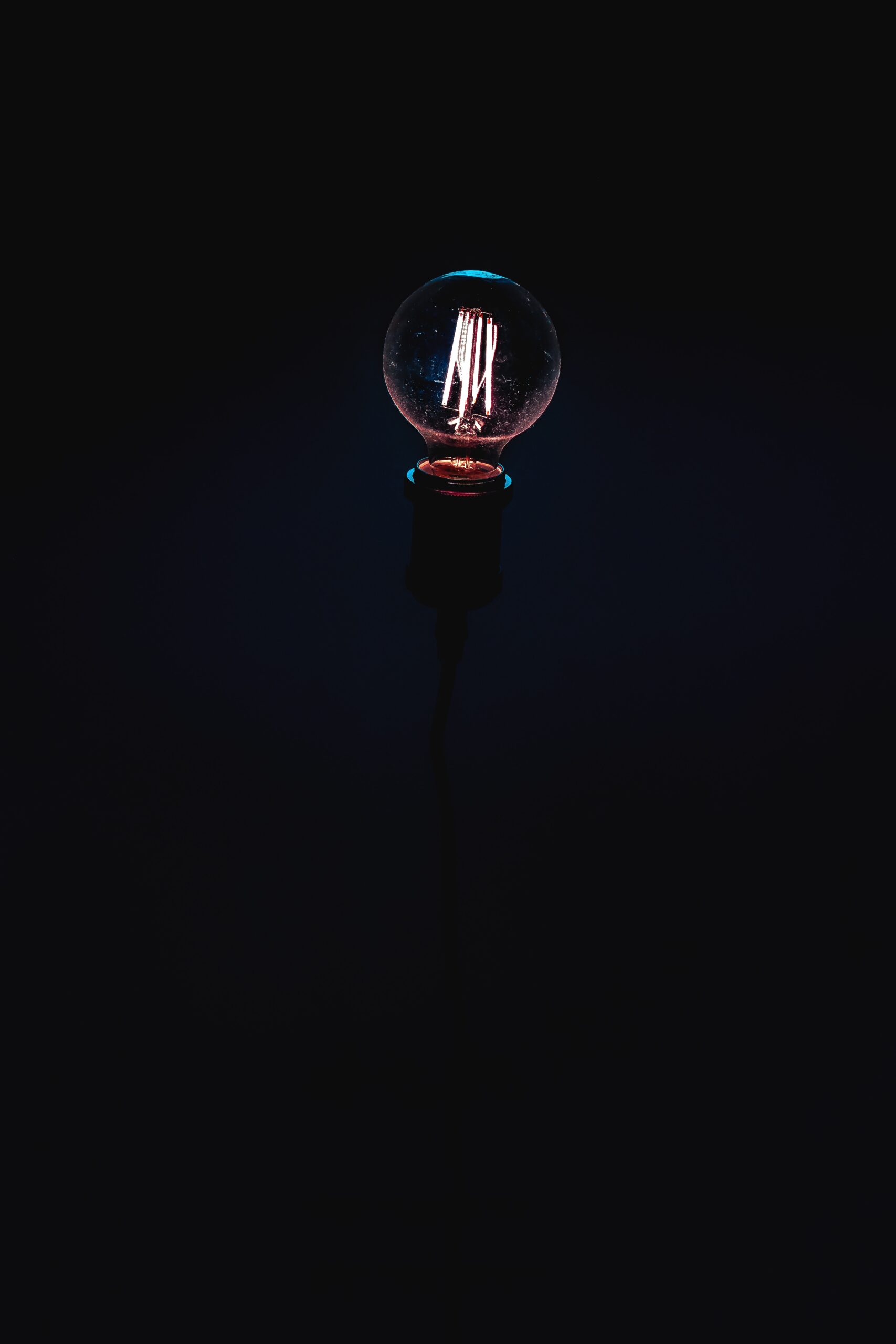
In this comprehensive guide, you will explore the fascinating world of TPU filament and gain a deep understanding of its properties, uses, and applications. TPU filament, also known as thermoplastic polyurethane, is a flexible and durable material widely used in 3D printing. Whether you’re a beginner or an experienced user, this guide aims to provide you with the knowledge and insights needed to navigate the world of TPU filament successfully. Get ready to unlock the potential of this versatile material and take your 3D printing projects to the next level.
1. What is TPU Filament?
1.1 Definition and Composition
TPU filament, or Thermoplastic Polyurethane filament, is a type of flexible and elastic material used in 3D printing. It is a popular choice for producing objects that require durability, flexibility, and resistance to wear and tear. TPU filament is made up of a thermoplastic polymer that combines the properties of both plastic and rubber.
1.2 Understanding Thermoplastic Polyurethane
Thermoplastic Polyurethane (TPU) is a versatile material that is commonly used in various industries such as automotive, footwear, electronics, and more. It is a class of polyurethane plastics that can be melted and solidified repeatedly without degrading their physical properties. TPU has excellent tensile strength, elongation characteristics, and resistance to oil, grease, and abrasion.
1.3 Properties and Applications of TPU Filament
TPU filament exhibits a range of unique properties that make it suitable for a wide range of applications. It has high flexibility, allowing it to be stretched and bent without breaking. This flexibility makes TPU filament ideal for producing objects such as phone cases, shoe soles, and flexible parts in mechanical systems.
TPU filament also offers high impact resistance, meaning it can withstand sudden shocks or impacts without deforming or cracking. This property is beneficial for applications such as protective gear, automotive parts, and industrial components.
Additionally, TPU filament exhibits excellent chemical and environmental resistance, making it suitable for outdoor applications or exposure to harsh chemicals. It is resistant to oil, grease, and various solvents, ensuring the longevity of printed objects in demanding environments.
The wide range of durometer options available for TPU filament allows users to tailor the material’s hardness to their specific requirements. Durometer refers to the hardness of a material, and TPU filament can be produced in both soft and hard variants, providing flexibility in design possibilities. Soft TPU filaments can be used for applications such as grips, seals, and cushioning, while harder variants are suitable for structural components.
Furthermore, TPU filament is compatible with different 3D printers, making it accessible to a wide range of users. Whether you have a FDM printer, a resin printer, or a selective laser sintering (SLS) printer, there is likely a TPU filament formulation available that can work well with your specific printer.
2. Advantages of TPU Filament
2.1 Flexible and Elastic Nature
One of the primary advantages of TPU filament is its flexibility and elastic nature. It can be bent, twisted, and stretched without risk of breaking or tearing. This property makes TPU filament ideal for applications that require objects to withstand deformation or repeated movement, such as hinges, gaskets, and flexible joints.
2.2 High Impact and Abrasion Resistance
TPU filament offers high impact resistance, meaning it can absorb and dissipate energy upon impact without deforming or breaking. This property makes it suitable for applications where durability is crucial, such as protective cases, shock absorbers, and machine parts subject to heavy use or potential collisions.
Additionally, TPU filament is highly resistant to abrasion, allowing it to withstand friction and wear over time. This resistance makes it suitable for applications such as conveyor belts, seals, and grips that come into contact with abrasive surfaces.
2.3 Chemical and Environmental Resistance
Another significant advantage of TPU filament is its resistance to a wide range of chemicals and environmental conditions. It can withstand exposure to oils, greases, solvents, and UV radiation without degrading or losing its integrity. This resistance makes TPU filament suitable for outdoor applications, as well as those involving contact with oils, chemicals, or harsh environments.
2.4 Wide Range of Durometer Options
TPU filament is available in a wide range of durometer options, allowing users to select the appropriate hardness for their specific application. Softer variants offer enhanced flexibility and elasticity, while harder variants provide increased rigidity and structural integrity. This versatility in durometer options makes TPU filament a versatile material that can be tailored to diverse printing needs.
2.5 Compatibility with Different 3D Printers
TPU filament is compatible with various 3D printers, including FDM, resin, and SLS printers. This compatibility ensures that users can easily incorporate TPU filament into their existing printing setup without the need for specialized equipment. Additionally, the compatibility with different printers allows for greater accessibility and versatility in creating prints with TPU filament.
This image is property of images.unsplash.com.
3. Disadvantages of TPU Filament
3.1 Difficulty in Printing
One of the challenges users may encounter when working with TPU filament is the difficulty in printing compared to traditional rigid filaments. Due to the flexible nature of TPU filament, it requires specific settings and adjustments to achieve successful prints. Users may need to fine-tune their printer settings, such as adjusting the printing speed, retraction settings, and temperature, to optimize the printing process with TPU filament.
3.2 Warping and Dimensional Accuracy
TPU filament can be prone to warping or shrinking during the printing process, which can affect the dimensional accuracy of the final print. It is important to ensure proper bed adhesion and temperature control to minimize the risk of warping. Additionally, achieving precise dimensional accuracy with TPU filament may require fine adjustments to the printer settings and careful attention to the printing environment.
3.3 Limited Color Options
Compared to some other filaments, such as PLA or ABS, TPU filament generally has a more limited color palette. This limitation is due to the complexity of achieving vibrant and consistent colors in the flexible TPU material. However, there are still a variety of standard colors available, including black, white, and various shades of gray, that can meet many printing needs.
3.4 Comparatively Higher Cost
TPU filament tends to be more expensive compared to some other commonly used filaments, such as PLA. The higher cost is primarily attributed to the production process and the specific properties of TPU filament. While the initial investment may be higher, the superior characteristics of TPU filament can justify the cost for applications that require its unique properties.
3.5 Post-processing Challenges
Post-processing TPU filament prints can present challenges compared to rigid materials. For example, removing support structures from TPU prints may require extra care and attention to avoid damaging the printed object. Additionally, sanding or smoothing the surface of TPU prints may require different techniques compared to rigid filaments due to its flexibility and elasticity.
4. Choosing the Right TPU Filament
4.1 Filament Diameter and Compatibility
When choosing TPU filament, it is essential to consider the filament diameter and compatibility with your 3D printer. Filament diameters typically range from 1.75mm to 3mm, so it is crucial to select the diameter that matches your printer’s specifications. Additionally, verify that your printer is capable of printing with flexible filaments and has the necessary extruder setup to handle TPU filament.
4.2 Durometer and Shore Hardness
Consider the desired hardness of the final print when selecting TPU filament. Soft TPU filaments with lower durometer ratings, such as Shore 60A, provide enhanced flexibility and elasticity. On the other hand, harder TPU filaments with higher durometer ratings, such as Shore 95A, offer increased rigidity and structural integrity. Choosing the appropriate durometer ensures that the printed object will have the desired properties for its intended application.
4.3 Pigmentation and Translucency
TPU filament is available in various levels of pigmentation and translucency. While standard opaque colors are commonly used, translucent and semi-transparent options can provide unique aesthetic possibilities. Consider the desired appearance and functionality of the final print when selecting the level of pigmentation and translucency.
4.4 Specialty TPU Filaments
In addition to standard TPU filaments, there are specialty TPU filaments available that offer specific properties or characteristics. For example, conductive TPU filaments can be used for applications involving electrical conductivity, such as electronic components or sensors. Similarly, flame-retardant TPU filaments are designed to resist flames and meet specific safety requirements. Consider whether any specialty TPU filaments can meet the specific needs of your project.
This image is property of images.unsplash.com.
5. Preparing for TPU Filament Printing
5.1 Printer Setup and Calibration
Before printing with TPU filament, ensure that your 3D printer is properly set up and calibrated. Check the printer’s extruder tension and make any necessary adjustments to accommodate the flexibility of TPU filament. Additionally, ensure that the printer’s build plate is leveled correctly to prevent issues with bed adhesion.
5.2 Bed Adhesion Methods
Since TPU filament has a flexible and elastic nature, achieving good bed adhesion can be challenging. Consider using adhesive aids such as a heated bed, a build surface with textured patterns or adhesion-promoting substances like glue or hairspray. Proper bed adhesion is vital to prevent warping or detachment during printing.
5.3 Recommended Print Settings
To achieve successful prints with TPU filament, it is advisable to use specific print settings. A slower print speed helps ensure accurate deposition of the flexible material and minimizes the risk of extrusion issues. Adjusting the retraction settings, including reducing retraction distance and speed, can also help prevent oozing or stringing.
Furthermore, optimizing the printing temperature is crucial for TPU filament. The recommended temperature range typically falls between 200°C and 240°C, but experimentation may be necessary to find the optimal temperature for your specific TPU filament brand.
5.4 Using Support Structures
In some cases, support structures may be required when printing with TPU filament. However, removing support structures from flexible prints can be challenging and may leave marks or damage the printed object. Consider utilizing dissolvable support materials or designing the print in a way that minimizes the need for support structures.
5.5 Post-print Cooling and Handling
After the printing process is complete, it is important to allow TPU filament prints to cool down naturally before removing them from the build plate. This cooling time helps minimize the risk of deformation or warping due to the residual heat. When handling TPU prints, be cautious to avoid unnecessary stretching or bending that could potentially deform the object.
6. Troubleshooting common TPU Filament Printing Issues
6.1 Stringing and oozing
Stringing and oozing are common issues encountered when printing with TPU filament. To mitigate these issues, reduce the printing speed to minimize the movement of the flexible material during printing. Additionally, adjusting the retraction settings, such as reducing retraction distance and speed, can help prevent excess material from extruding during travel moves.
6.2 Filament Tangles and Snags
Due to the flexible nature of TPU filament, it can sometimes tangle or snag during the printing process. Ensure that the filament is properly guided into the extruder to prevent entanglement or snags. Additionally, using a filament guide or dry box can help minimize filament handling issues and maintain the quality of the filament.
6.3 Layer Adhesion Problems
Poor layer adhesion can occur with TPU filament, resulting in weak parts or delamination. To improve layer adhesion, consider increasing the printing temperature slightly to ensure proper fusion between each layer. Experimenting with different infill patterns and densities can also enhance layer bonding and overall part strength.
6.4 Warping and Delamination
Warping and delamination can occur when printing larger or more complex TPU filament objects. To minimize these issues, use an adhesive aid such as a heated bed with proper bed leveling. Additionally, enclosing the printer or using a print chamber can help maintain a consistent temperature throughout the printing process, reducing the likelihood of warping or delamination.
6.5 Print Surface Imperfections
Print surface imperfections, such as uneven surfaces or inconsistent layer heights, can occur when printing with TPU filament. Ensuring a level and properly calibrated printer bed, as well as optimizing the first layer settings, can help achieve a smooth and even print surface. Adjusting the print speed, flow rate, or nozzle height can also assist in addressing surface imperfections.
This image is property of images.unsplash.com.
7. Post-processing and Finishing Techniques
7.1 Removing Support Structures
After printing with TPU filament, removing support structures can be challenging due to the flexible nature of the material. Consider using support materials that can be dissolved or broken away easily, minimizing the risk of damaging the printed object.
7.2 Sanding and Smoothing the Surface
Sanding and smoothing the surface of TPU filament prints requires different techniques compared to rigid materials. Due to the elastic nature of TPU filament, traditional abrasive sanding methods may not be as effective. Consider using sanding sponges or flexible sanding tools to gently smooth the surface without causing deformation or distortion.
7.3 Painting and Coloring Options
While TPU filament may have limited color options compared to other filaments, it is still possible to paint or add color to your TPU prints. Acrylic paints and flexible paint formulations can be used to add vibrant colors or patterns to TPU objects. Testing the paint on a small area of the print or using a primer can help ensure compatibility and adhesion.
7.4 Clear Coating and Gloss Enhancement
To enhance the appearance and provide additional protection, clear coatings or gloss finishes can be applied to TPU filament prints. Spray-on clear coat formulations designed for flexible materials can be used to provide a glossy or semi-glossy finish. Proper surface preparation, including cleaning and drying the print, is crucial for achieving a smooth and even coating.
7.5 Post-print Strength and Flexibility Enhancements
If additional strength or flexibility is desired for TPU filament prints, post-print treatments can be employed. Techniques such as annealing or heat treatment can increase the overall strength and rigidity of TPU objects. Experimentation with different post-processing techniques can help achieve the desired mechanical properties for specific applications.
8. TPU Filament Applications
8.1 Consumer Products
TPU filament finds numerous applications in the production of consumer products. Its flexibility, durability, and resistance to wear make it an ideal material for phone cases, earphone covers, watch straps, and other personal accessories. TPU’s ability to withstand impact and provide shock absorption also makes it suitable for protective gear such as helmets, knee pads, and phone bumpers.
8.2 Automotive and Aerospace
In the automotive and aerospace industries, TPU filament is valued for its high impact resistance and flexibility. It can be used to produce durable gaskets, seals, and vibration dampeners. TPU’s resistance to oil, grease, and various chemicals also makes it suitable for automotive hoses, tubing, and connectors that require resistance to harsh fluids.
8.3 Medical and Healthcare
TPU filament has gained popularity in the medical and healthcare fields due to its biocompatibility and resistance to sterilization methods. It is used to manufacture a wide range of applications, including braces, prosthetics, splints, medical device components, and orthopedic insoles. TPU’s flexibility and elasticity make it particularly beneficial for comfort and patient mobility in these applications.
8.4 Sports and Recreation
TPU filament is widely used in sports and recreational applications due to its impact resistance, flexibility, and durability. It is utilized in the production of shoe soles, sportswear, and athletic equipment such as knee pads, mouth guards, and bike grips. TPU’s ability to provide cushioning and shock absorption makes it valuable for applications that involve high impact or repeated movement.
8.5 Industrial Prototyping and Manufacturing
In the field of industrial prototyping and manufacturing, TPU filament is utilized for producing functional prototypes and end-use parts. Its flexibility, high impact resistance, and resistance to wear and tear make it suitable for creating functional components such as gears, bushings, seals, and connectors. TPU’s ability to withstand environmental factors and its chemical resistance are also beneficial for industrial applications.
9. Future Trends and Developments
9.1 Innovations in TPU Filament
As the field of 3D printing continues to evolve, innovations in TPU filament are expected. Companies are investing in research and development to enhance the overall performance and expand the range of TPU filaments available. Innovations may involve improved printing characteristics, increased material strength, and the introduction of specialized TPU formulations for specific applications.
9.2 Biodegradable TPU Filaments
Environmental concerns have led to the development of biodegradable TPU filaments. These filaments aim to provide the unique properties of TPU while also addressing sustainability concerns. Biodegradable TPU filaments can reduce the environmental impact of printing with TPU and broaden its application possibilities in eco-friendly industries.
9.3 Advanced 3D Printing Techniques
Advancements in 3D printing technology are expected to further improve the printing process for TPU filaments. This includes the development of advanced extruders, specialized nozzles suited for TPU materials, and improved printer firmware to optimize printing settings. These developments can enhance the user experience, increase print success rates, and promote the further adoption of TPU filament.
9.4 Material Compatibility and Combinations
Future developments may focus on the compatibility and combination of TPU filament with other 3D printing materials. This can open up new possibilities for creating hybrid prints that combine the strengths of different materials. For example, printing TPU with rigid filaments like PLA or ABS can create objects that have rigid structures with flexible components, expanding the versatility and functionality of 3D printed parts.
10. Conclusion
10.1 Recap of TPU Filament Characteristics
TPU filament, or Thermoplastic Polyurethane filament, offers a range of unique properties that make it a versatile material for 3D printing. It combines flexibility, elasticity, high impact resistance, and resistance to chemicals and wear. TPU filament is compatible with various 3D printers and comes in a wide range of durometer options to suit different applications.
10.2 Final Thoughts and Recommendations
When working with TPU filament, it is important to understand its properties and requirements for successful printing. Proper printer setup, adjustment of print settings, and careful handling during post-processing are crucial for achieving high-quality prints. By considering the specific requirements of your project and selecting the appropriate TPU filament, you can harness the unique benefits of this material for a wide range of applications.
Overall, TPU filament presents exciting possibilities for creating functional and durable objects in industries ranging from consumer products to automotive and healthcare. As advancements continue to shape the field of 3D printing and TPU filament technology, we can expect to see further innovations and expanded applications for this versatile material.