What You Should Know About ABS 3D Printing
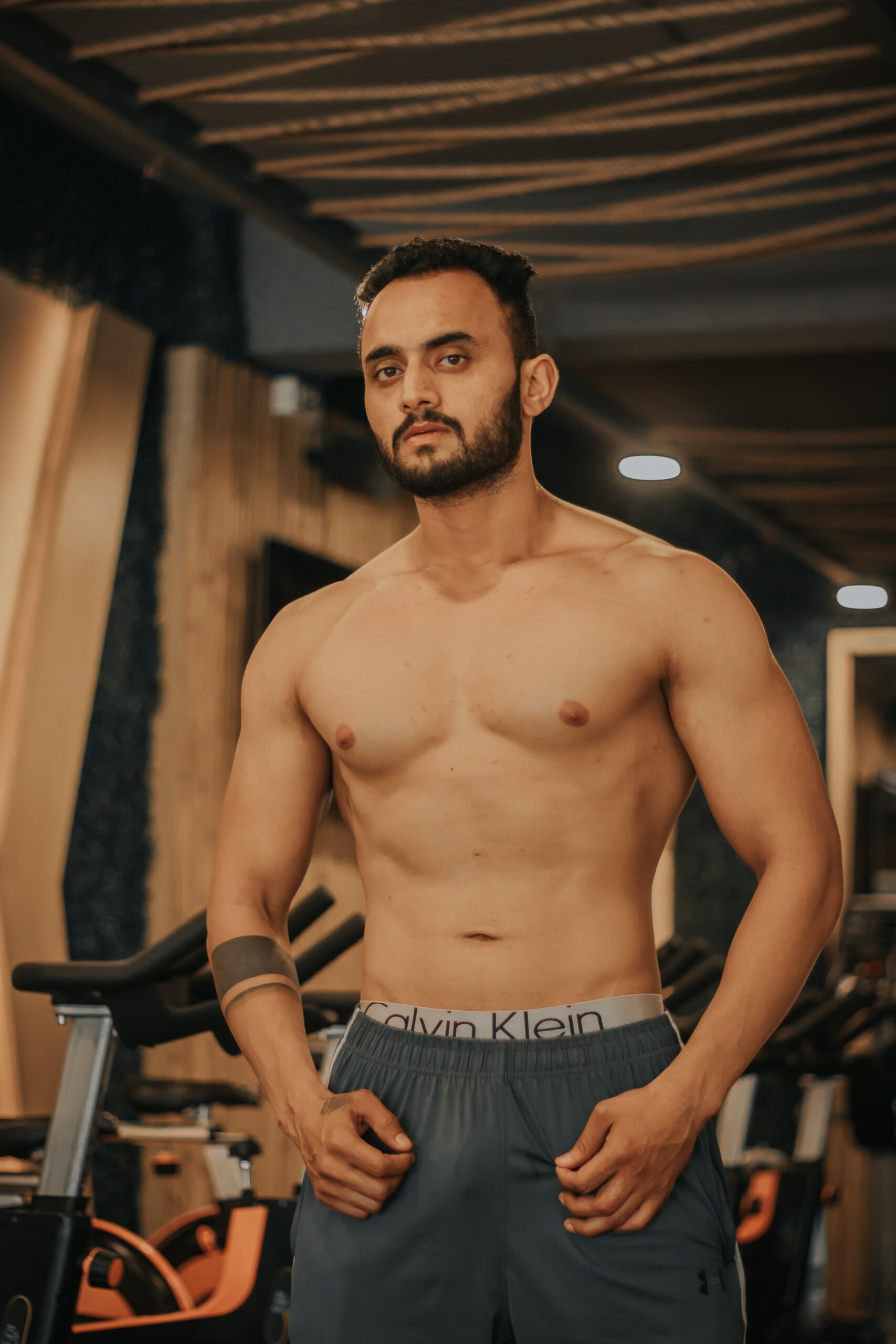
If you’ve ever been curious about 3D printing, then ABS 3D printing is definitely something you should know about. ABS, short for Acrylonitrile Butadiene Styrene, is a type of plastic commonly used in 3D printing. In this article, we’ll explore what ABS 3D printing is, how it works, and why it’s gaining popularity in various industries. So, grab a cup of coffee and get ready to dive into the fascinating world of ABS 3D printing!
This image is property of images.unsplash.com.
What is ABS 3D Printing
ABS 3D printing, or Acrylonitrile Butadiene Styrene 3D printing, is a popular additive manufacturing technique that uses ABS filament as the raw material to create three-dimensional objects. ABS is a thermoplastic polymer known for its excellent mechanical properties, making it a preferred choice for a wide range of applications. In ABS 3D printing, layers of molten ABS filament are deposited one on top of another to gradually build the desired object. ABS 3D printing has gained significant popularity in various industries, including engineering, manufacturing, and art, due to its strength, durability, and versatility.
Advantages of ABS 3D Printing
Strong and Durable
ABS 3D printing offers exceptional strength and durability, making it suitable for applications that require robust and impact-resistant parts. The printed objects exhibit high tensile strength, allowing them to withstand external forces without easily breaking. This advantage is particularly useful in industries such as automotive, aerospace, and consumer goods, where strength and durability are vital requirements.
Good Heat Resistance
ABS filament possesses excellent heat resistance properties, allowing it to withstand moderate temperatures without deforming or melting. This characteristic is essential for applications that involve exposure to heat or require functional parts to withstand high temperatures, such as automotive components, electrical enclosures, and household appliances.
Easy to Work With
ABS filament is known for its ease of use and versatility in 3D printing. It melts at a relatively low temperature, which makes it compatible with a wide range of 3D printers. Additionally, ABS is easy to manipulate and post-process, allowing for effortless sanding, drilling, and painting of the printed objects. This ease of workability makes ABS an ideal choice for both beginners and experienced users in the 3D printing community.
Wide Range of Colors
ABS filament is available in a wide array of vibrant colors, allowing for creative and visually appealing 3D prints. This versatility in color options makes ABS 3D printing a popular choice in various applications, including artistic and decorative objects, architectural models, and educational tools. The ability to choose from a wide range of colors provides flexibility and enhances the aesthetic appeal of the final printed objects.
Affordable
ABS filament is one of the most affordable options for 3D printing, making it accessible to a larger user base. Its cost-effectiveness, combined with its excellent mechanical properties, makes ABS an attractive choice for both hobbyists and professionals. The affordability of ABS filament enables users to experiment, iterate, and create functional prototypes or finished products without breaking the bank.
Limitations of ABS 3D Printing
Warpage and Shrinkage
One of the primary limitations of ABS 3D printing is its tendency to warp and shrink during the printing process. As ABS filament cools down, it undergoes significant shrinkage, leading to the deformation of the printed object and potential warping. This issue can be mitigated by using a heated bed, enclosing the printer to maintain a stable temperature, and applying adequate bed adhesion techniques.
Requires Adequate Ventilation
ABS filament releases potentially harmful fumes when heated, making ventilation a crucial consideration during ABS 3D printing. It is important to operate the printer in a well-ventilated area or use ventilation systems to prevent the accumulation of fumes. Proper ventilation ensures the safety of the user and helps maintain air quality in the surrounding environment.
Not Suitable for Food-Grade Applications
ABS filament is not food-grade certified, meaning it is not safe for direct contact with food or beverages. As ABS 3D printed objects can harbor bacteria and may release chemicals that are not suitable for consumption, it is important to avoid using ABS for applications involving food or drinks. For food-grade applications, alternative filaments such as PLA (Polylactic Acid) are recommended.
Post-processing may be required
Although ABS filament produces durable and strong prints, the surface finish may not always be smooth and ready for use. Depending on the desired outcome, ABS prints may require post-processing techniques such as sanding, smoothing, or applying surface treatments to achieve the desired level of aesthetics and functionality. It is important to be prepared for additional post-processing steps to optimize the final quality of ABS printed objects.
Understanding ABS Filament
Composition and Materials
ABS filament is composed of three main components: acrylonitrile, butadiene, and styrene. These materials combine to form a strong and durable thermoplastic polymer that is suitable for 3D printing. The acrylonitrile component provides the rigidity and chemical resistance, while the butadiene component enhances the impact resistance and toughness. The styrene component contributes to the overall stability and processability of the filament.
Different ABS Filament Grades
ABS filament is available in various grades, each with specific properties and characteristics. Some common ABS grades include standard ABS, ABS with added additives for improved strength or heat resistance, and ABS composites with added materials like carbon fiber or metal particles for enhanced mechanical properties. Choosing the appropriate ABS filament grade depends on the specific requirements of the intended application.
Filament Diameter and Tolerance
ABS filament comes in different diameters, typically ranging from 1.75mm to 3mm. It is important to select the filament diameter that matches the specifications of the 3D printer being used. Additionally, filament tolerance refers to the allowable variance in diameter, and it is crucial to ensure that the filament is within the specified tolerance range for optimal printing results.
This image is property of images.unsplash.com.
Printing Parameters for ABS
Bed Temperature
ABS filament requires a heated bed to minimize the risk of warping and promote proper adhesion to the print surface. The recommended bed temperature for ABS 3D printing typically ranges from 80°C to 110°C, depending on the specific printer and filament being used. It is important to adjust the bed temperature accordingly to achieve successful prints.
Nozzle Temperature
The ideal nozzle temperature for ABS filament lies between 220°C to 250°C, again depending on the specific printer and filament. The higher nozzle temperature ensures that the ABS filament melts consistently and flows smoothly during the printing process. It is essential to fine-tune the nozzle temperature based on the manufacturer’s recommendations and personal experience.
Print Speed and Layer Height
When printing with ABS filament, it is important to carefully consider the print speed and layer height settings. Slower print speeds allow for better layer adhesion and reduce the likelihood of warping. Typically, a print speed of around 30-60mm/s is recommended for ABS printing. Choosing the appropriate layer height is crucial to achieving the desired level of detail and surface finish.
Print Surface Preparation
To ensure proper adhesion, the print surface needs to be adequately prepared. Applying a layer of adhesive, such as a glue stick or ABS-specific adhesive solution, can help promote adhesion and prevent warping. Some users also utilize specialized print surface materials like PEI sheets or BuildTak for improved adhesion and ease of print removal.
Printing Enclosures
Enclosing the 3D printer during ABS printing can help maintain a stable printing environment and minimize temperature fluctuations. Printing enclosures, whether commercially available or DIY, help trap heat and reduce the risk of warping and cracking. Enclosures also aid in controlling the airflow around the printed object, ensuring consistent cooling and minimizing the potential for warpage.
Tips for Successful ABS 3D Printing
Use a Heated Bed
To minimize warping and promote adhesion, ensure that your 3D printer has a heated bed and set it to the appropriate temperature for ABS filament. A heated bed helps to maintain a consistent temperature throughout the printing process.
Enclose the Printer
Consider enclosing your 3D printer to create a controlled environment that reduces temperature fluctuations and drafts. Enclosures help maintain a stable temperature, reducing the risk of warping and improving print quality, especially when printing large or complex ABS objects.
Choose the Appropriate Nozzle Size
Selecting the right nozzle size can affect print quality and efficiency. Larger nozzle diameters can provide faster prints but may sacrifice certain details. Smaller nozzle diameters offer greater precision but may result in slower print times. Consider the specific requirements of your project and select the appropriate nozzle size accordingly.
Optimize Printing Speed
Adjusting the print speed can significantly impact the quality and strength of ABS prints. Slower print speeds allow for better layer adhesion, reducing the risk of warping and improving the overall print quality. Experiment with different print speeds to find the optimum balance between quality and efficiency.
Apply Adequate Cooling
While ABS benefits from a controlled printing environment, appropriate cooling is still necessary to prevent overheating and maintain dimensional accuracy. Ensure that your printer’s cooling settings are adjusted to provide the necessary cooling during the printing process. Find the right balance between cooling and maintaining a stable printing environment.
Work in a Well-Ventilated Area
ABS filament releases potentially harmful fumes when heated, so it is crucial to work in a well-ventilated area or use ventilation systems to maintain air quality. Avoid prolonged exposure to ABS fumes and consider installing filtration systems when working with ABS 3D printing.
Perform Regular Maintenance
Regular maintenance of your 3D printer is important to ensure consistent, high-quality prints. Keep your printer clean, lubricate moving parts, and regularly check and calibrate the bed level and nozzle height. Performing routine maintenance tasks helps to prevent issues such as nozzle clogs or misalignment, ensuring smooth and successful ABS 3D printing.
This image is property of images.unsplash.com.
Common Issues with ABS 3D Printing
Warping and Curling
Warping and curling occur when the printed object shrinks unevenly, causing it to detach from the print bed. This issue is frequently encountered with ABS filament due to its high shrinkage rate. Proper bed leveling, using a heated bed, and applying adhesive or additional bed adhesion techniques can help mitigate warping and curling.
Cracking and Splitting
ABS prints may experience cracking and splitting if the print settings result in excessive internal stresses during cooling. This can be caused by rapid cooling or insufficient cooling, leading to tensions within the printed object. Adjusting the cooling settings, such as fan speed and layer cooling time, can minimize the risk of cracking and splitting.
Delamination
Delamination refers to the separation of individual layers within a printed object, resulting in a weak and structurally compromised print. Inadequate bed adhesion or insufficient bonding between layers can cause delamination. Ensuring proper bed adhesion techniques, optimizing print temperature and speed, and using higher-quality ABS filament can minimize delamination issues.
Stringing and Oozing
Stringing and oozing are common issues in 3D printing that occur when the melted filament oozes or forms unwanted strings between separate parts of the print. Adjusting the retraction settings, such as retraction distance and speed, can help reduce stringing and oozing. Additionally, fine-tuning the nozzle temperature and print speed can also mitigate these issues.
Bubbling and Blobs
Bubbling and blobs can occur during ABS 3D printing when there are inconsistencies in the extrusion of the filament. This can result from issues such as uneven filament diameter, improper retraction settings, or inconsistent nozzle temperature. Ensuring a consistent filament diameter and optimizing retraction and temperature settings can minimize bubbling and blobs in printed objects.
Poor Bed Adhesion
Poor bed adhesion can lead to print failures, with the printed object detaching from the print bed during the printing process. This issue can occur due to inadequate bed leveling, insufficient use of adhesive, or an incorrect bed temperature. Properly leveling the bed, using adequate adhesion techniques, and adjusting the bed temperature can improve bed adhesion and prevent print failures.
Layer Separation
Layer separation occurs when the layers of an ABS print do not bond properly, leading to a weak and structurally compromised object. This problem can arise due to various factors, including improper print temperature, inadequate cooling, or excessive print speed. Fine-tuning the printing parameters, such as temperature, cooling, and print speed, can enhance layer bonding and reduce layer separation.
Quality of the Print
The overall quality of an ABS 3D print can be affected by various factors, including print settings, filament quality, and printer calibration. To achieve high-quality prints, it is essential to optimize the printing parameters, select high-quality ABS filament, and regularly calibrate and maintain the 3D printer. Experimentation, fine-tuning, and attention to detail can contribute to achieving the desired print quality.
Post-Processing ABS Prints
Sanding and Smoothing
Post-processing ABS prints often involves sanding and smoothing the surface to achieve a desired finish. Sanding can be done manually using different grits of sandpaper or with the help of sanding tools such as a Dremel. This process helps eliminate layer lines and imperfections, resulting in a smooth and refined surface quality.
Using Acetone Vapor
Acetone vapor smoothing is a post-processing technique commonly used with ABS prints. By exposing the printed object to acetone vapor, the surface of the ABS filament is melted, resulting in improved smoothing and blending of the layers. This technique can be performed using a small vapor chamber or by carefully controlling the exposure to acetone vapor.
Applying Surface Treatments
Surface treatments, such as priming or sealing with appropriate coatings, can enhance the aesthetics and functionality of ABS prints. Primers create a smooth base for painting, while sealants provide protection and improve resistance to chemicals or moisture. Choosing the right surface treatment based on the intended use and desired outcome can significantly enhance the final appearance of ABS prints.
Painting and Finishing
ABS prints can be painted and finished using various techniques to achieve the desired visual impact. Painting with acrylic or enamel paints, airbrushing, or using specialized painting techniques can transform the ABS prints into visually appealing objects. Additionally, adding details with decals or applying protective coatings can further enhance the overall appearance and durability of the finished prints.
Applications of ABS 3D Printing
Prototyping and Product Development
ABS 3D printing is widely used in prototyping and product development stages due to its strength, durability, and ease of post-processing. Its ability to withstand functional testing and simulate the properties of the final product makes ABS an ideal choice for rapid prototyping.
Functional Parts
ABS 3D printing is used to create functional parts for various industries, including automotive, aerospace, and electronics. Its strength, heat resistance, and flexibility allow for the production of durable and reliable components that can withstand demanding applications.
Artistic and Decorative Objects
ABS filament’s wide range of colors and ease of post-processing make it popular for creating artistic and decorative objects. Artists and designers use ABS 3D printing to bring their creative visions to life, producing intricate and visually stunning sculptures, figurines, and other decorative pieces.
Engineering and Mechanical Components
ABS 3D printing is commonly used in engineering and mechanical applications to produce custom parts, jigs, fixtures, and prototypes. Its strength, durability, and dimensional stability make it suitable for applications that require precise engineering tolerances and resistance to mechanical stresses.
Educational and Learning Tools
ABS 3D printing has found significant use in educational settings as a hands-on learning tool. It allows students to explore various concepts in engineering, design, and manufacturing, enabling them to visualize and materialize their ideas. ABS 3D printing helps foster creativity and problem-solving skills, making it a valuable tool in STEM education.
Safety Measures and Precautions
Proper Ventilation
When working with ABS filament, ensure that you operate the 3D printer in a well-ventilated area or use ventilation systems to remove potentially harmful fumes. Proper ventilation helps to maintain a safe working environment and minimize the inhalation of harmful gases emitted during the printing process.
Use of Personal Protective Equipment (PPE)
When handling ABS filament and during 3D printing, it is advisable to use appropriate personal protective equipment (PPE) such as gloves and safety goggles. PPE helps protect against possible skin and eye irritations that may arise from direct contact with the filament or exposure to fumes.
Avoidance of Direct Skin Contact
ABS filament may cause skin irritation or allergic reactions in some individuals. It is important to avoid direct skin contact with ABS filament and to wash hands thoroughly after handling the filament or printed objects. If irritation or allergic symptoms occur, discontinue use and seek medical advice if necessary.
Storage and Handling of ABS Filament
Proper storage and handling of ABS filament are essential for maintaining its quality and performance. ABS filament should be stored in a sealed container or vacuum-sealed packaging to prevent moisture absorption. It is important to keep the filament in a cool and dry environment to minimize the risk of degradation or printing issues.
Awareness of Fire Hazards
ABS filament is known to be flammable and poses a fire hazard if proper precautions are not taken. Avoid exposing ABS filament and printed objects to open flames, excessive heat sources, or hot surfaces. It is crucial to maintain a safe printing environment and have appropriate fire detection and extinguishing systems in place to mitigate fire risks.
In conclusion, ABS 3D printing offers a range of advantages, including its strength, heat resistance, ease of use, wide color selection, and affordability. However, it is important to be aware of the limitations and challenges associated with ABS printing, such as warping, ventilation requirements, unsuitability for food-grade applications, and the potential need for post-processing. Understanding the composition and properties of ABS filament, as well as optimizing printing parameters, can greatly contribute to successful ABS 3D printing. By following proper safety measures and precautions, unlocking the potential of ABS 3D printing becomes an exciting and rewarding journey with numerous applications across various industries and educational settings.